Bachelor's thesis: duration – 1 semester, finished – 16/6/2017
• BUT Rector’s Award, model exhibited – DESIGN.S 2018
BRIEF
Design a hot-melt glue gun with mechanical glue displacement intended for DIY enthusiasts. Improve the usability, aesthetics and ergonomics of the glue gun.
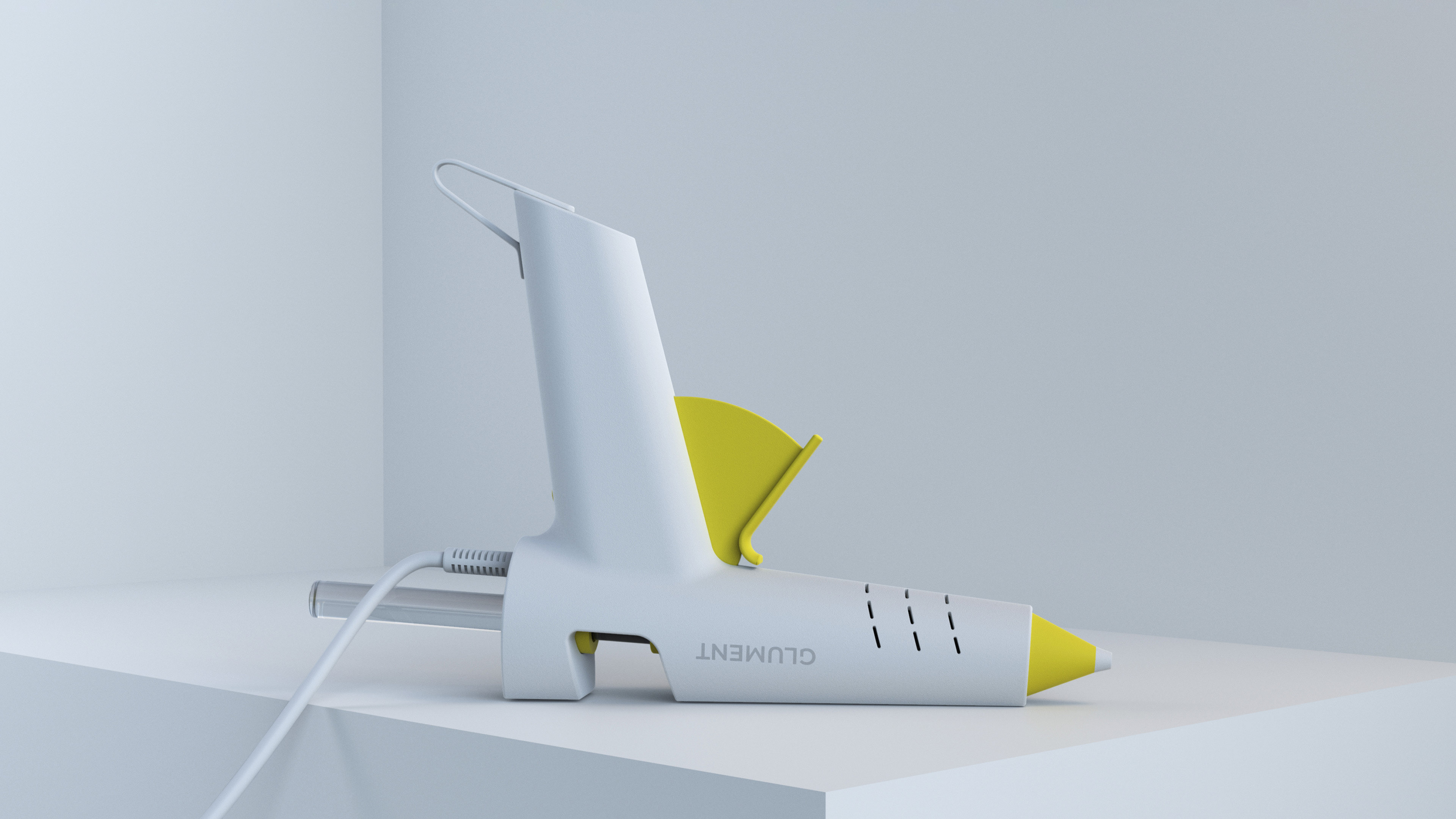
STARTING POINT
• I analyzed the ergonomics and internal architecture of the existing products.
• I defined my target audience – DIY enthusiasts of all genders of productive age.
• I defined my target audience – DIY enthusiasts of all genders of productive age.
I focused on the ergonomics and ease of use of the glue gun, and identified 3 possible directions for the shape.
PROBLEM IDENTIFICATION
• lack of an indicator to show when the glue gun is ready to use
• lack of temperature settings to allow the user to use more than one type of glue
• heavy power cord reduces stability when glue gun is placed on folding stand
• cheaper options tend to overheat and damage the glue gun
• lack of temperature settings to allow the user to use more than one type of glue
• heavy power cord reduces stability when glue gun is placed on folding stand
• cheaper options tend to overheat and damage the glue gun
• glue drips when not in use
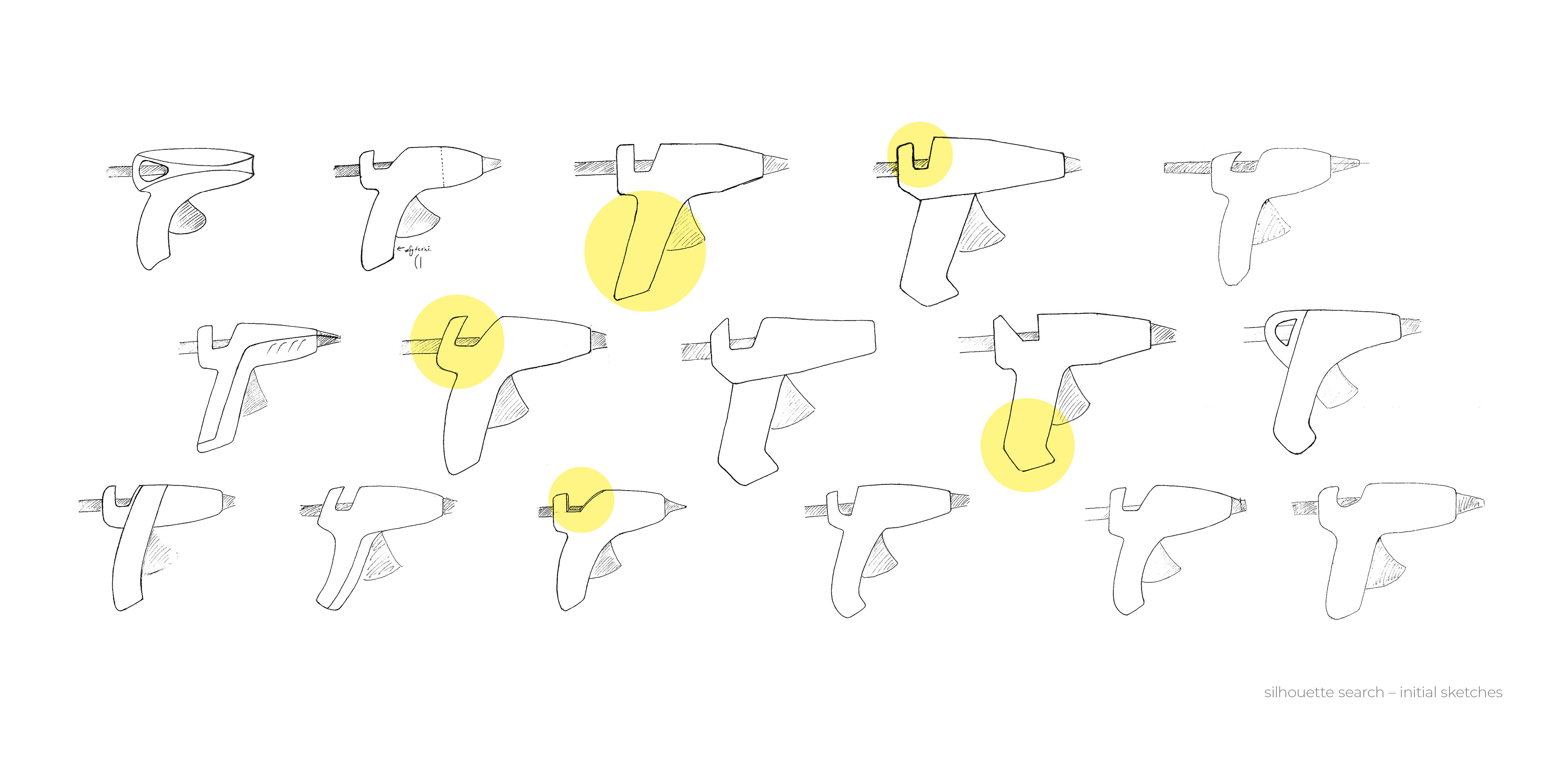
CONCEPT DEVELOPMENT
The next step was to turn these concepts into clay models. I tested different angles between the body and the handle, and different cross-sections to make it comfortable to work with.
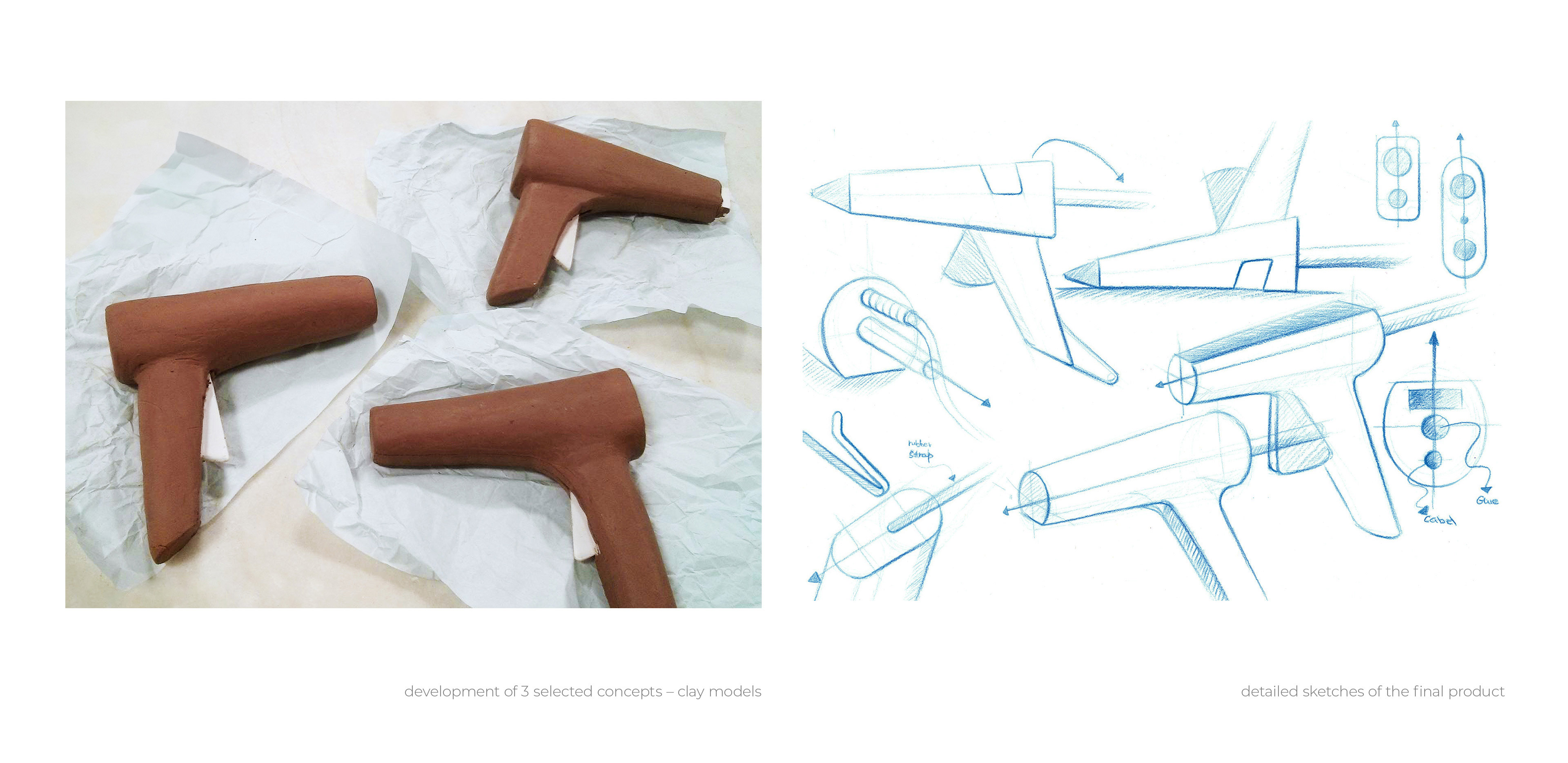
FINAL design
The form of the final design is the result of the problem-solving process. The idea was to remove the unstable folding stand and use the upper part of the body as a stand.
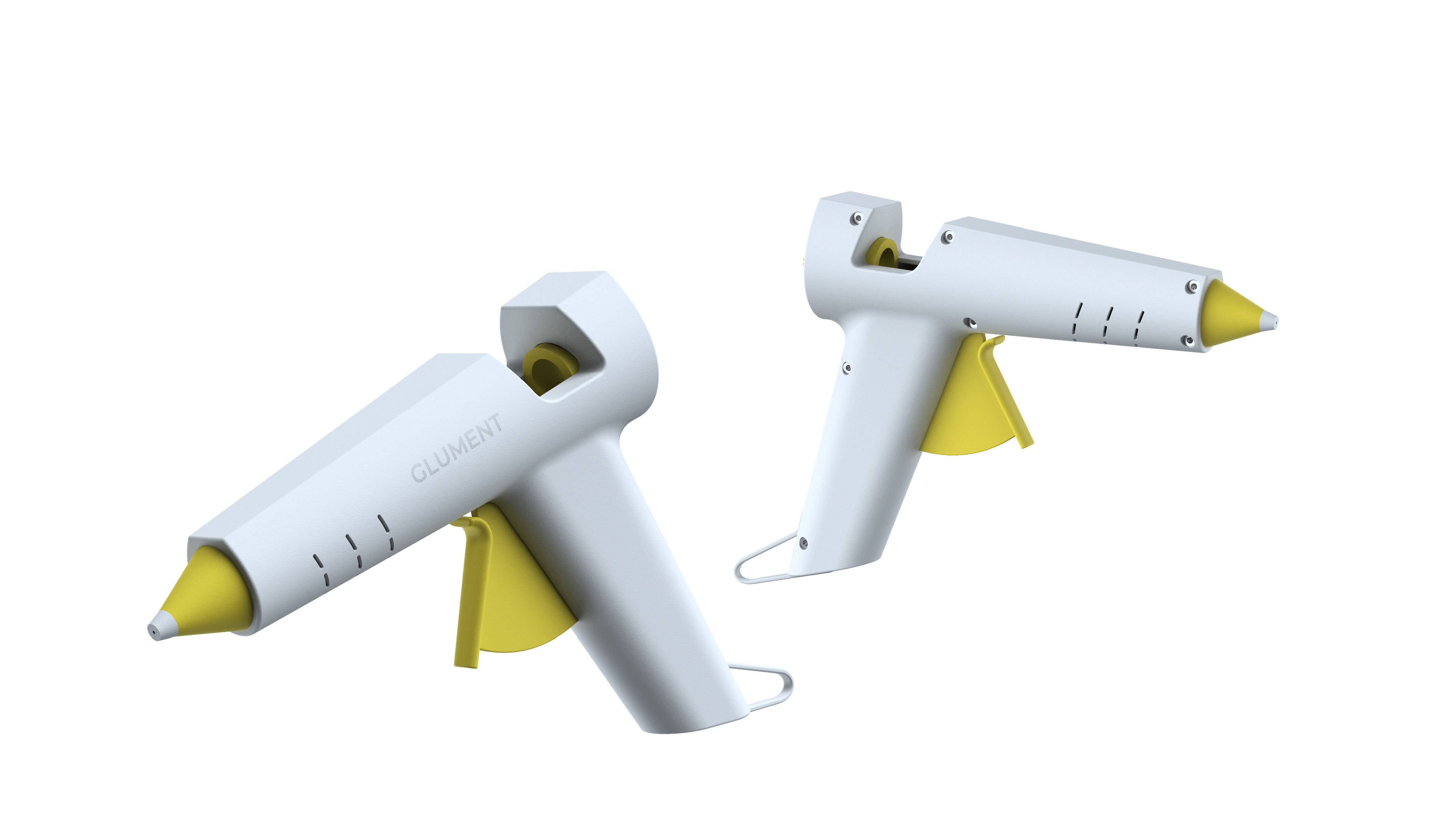
DETAILS
The LED indicator shows when the glue gun is ready for use. A control knob allows the user to adjust the heating temperature displayed on the LCD display.
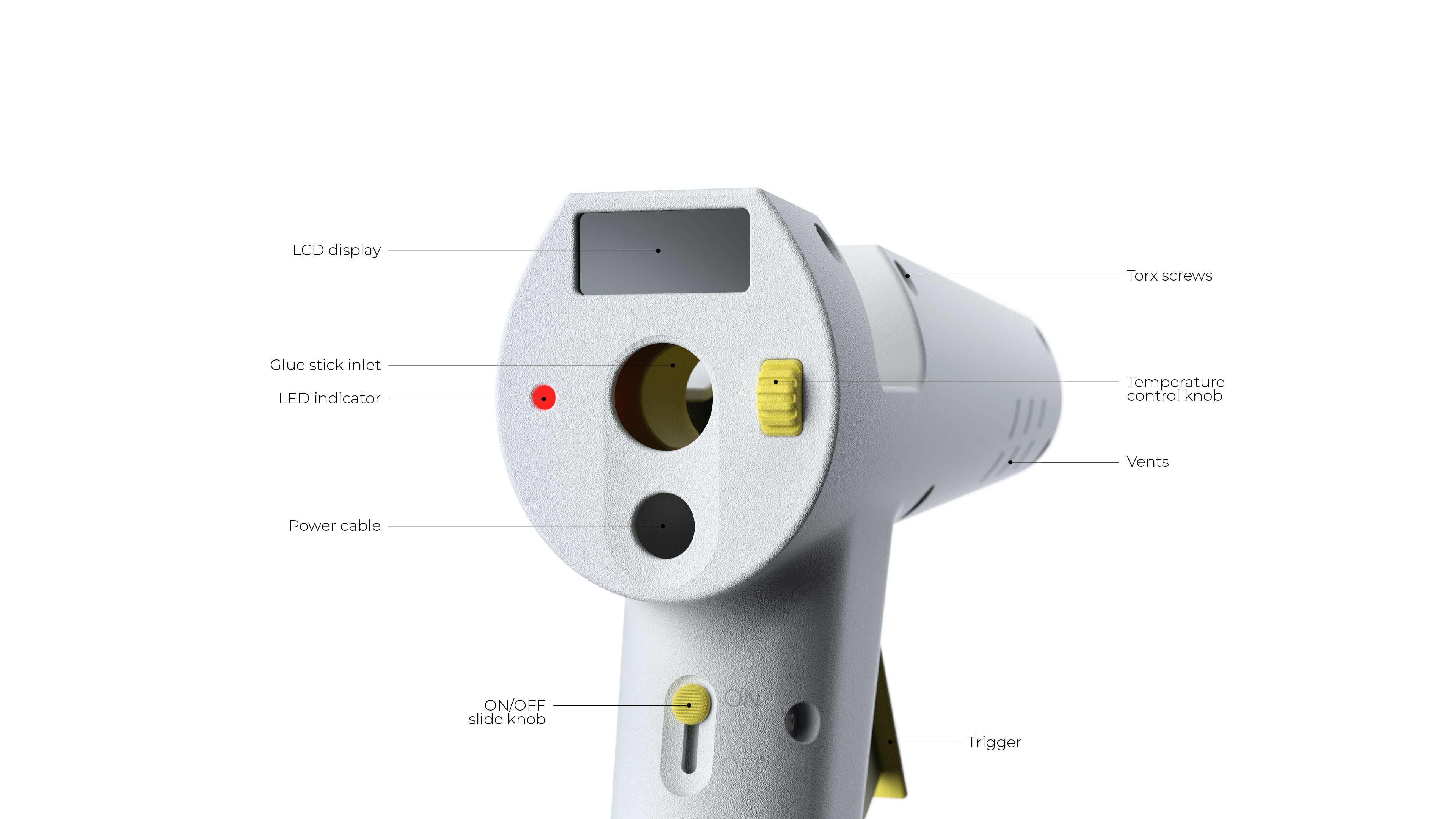
core idea and ERGONOMICS
• the upper part of the body was turned into a stand. To lower the center of gravity, the power cable was moved downwards
• during testing, I also noticed that the glue dripped less in this position when not in use
• during testing, I also noticed that the glue dripped less in this position when not in use
• the size of the handle is based on anthropometric measurements for the average person (50th percentile)
• after several tests with clay models, I chose a 105° angle between the body and the handle of the glue gun
• after several tests with clay models, I chose a 105° angle between the body and the handle of the glue gun
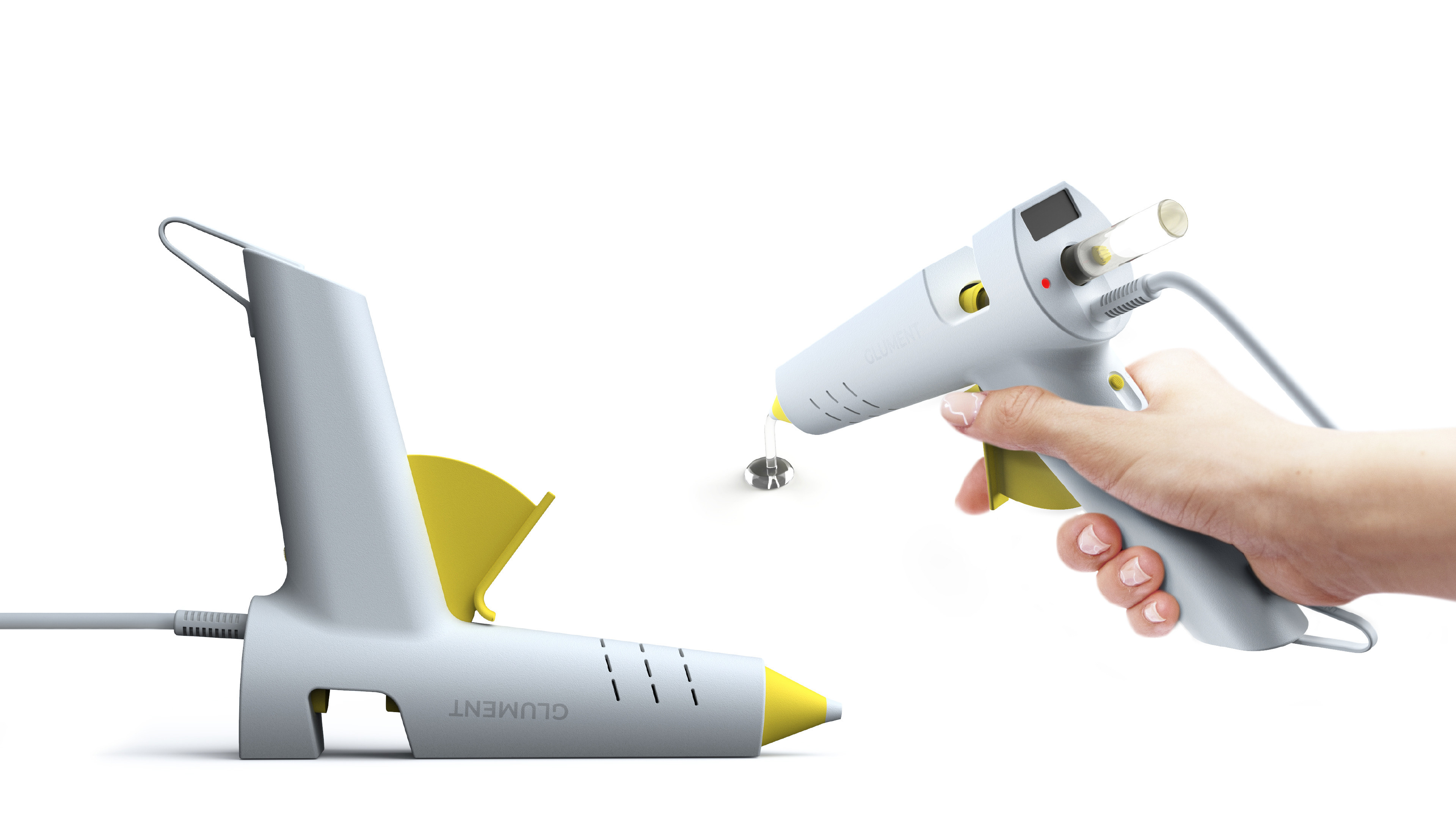
DIMENSIONS / Product architecture
The size of the designed product makes it easy to grip and handle.
Torx screws connect housings together.
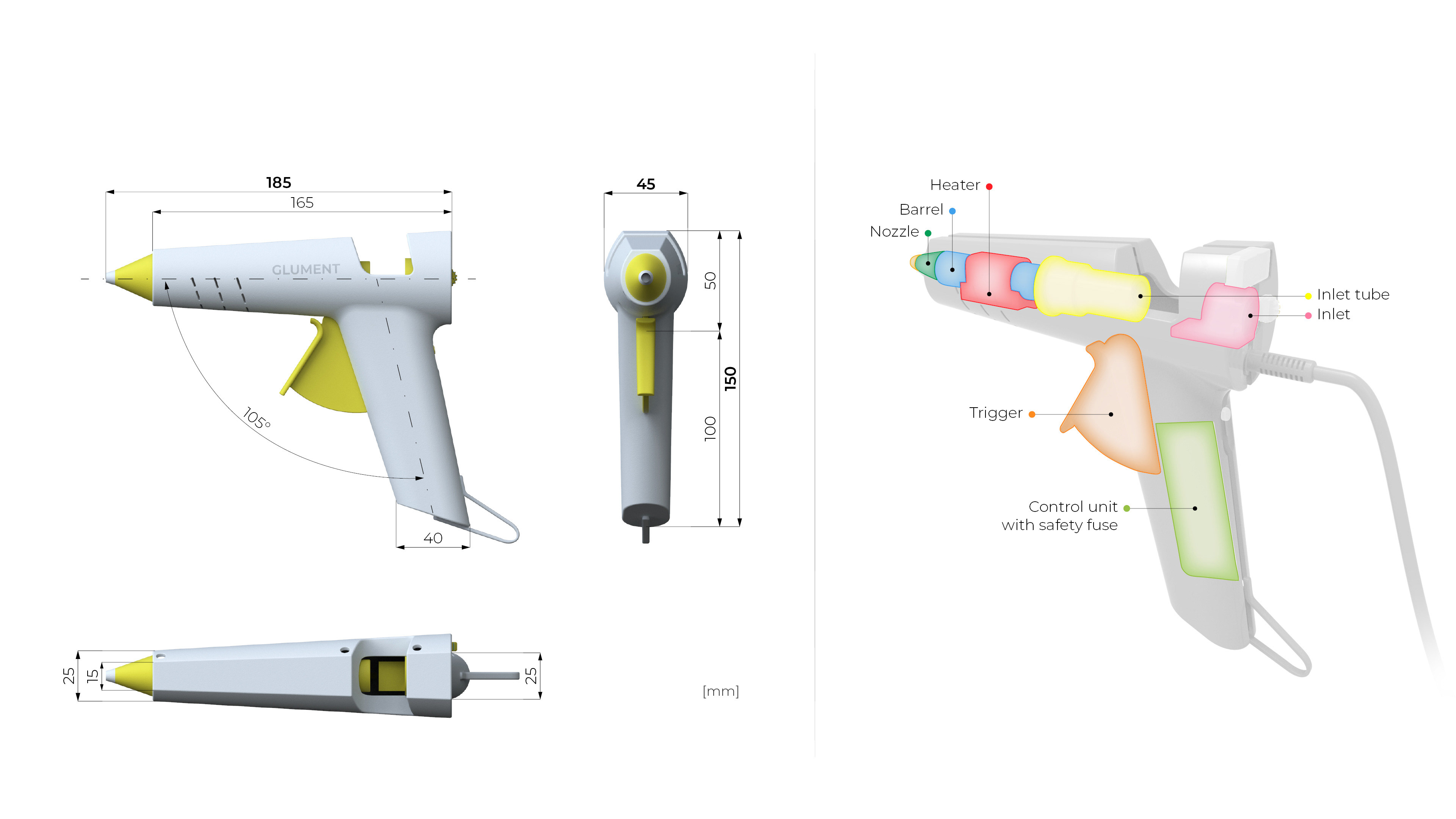
MATERIALS and manufacturing process
ABS plastic was chosen for this product because it is tough, ductile and heat resistant and has low manufacturing costs. In the case of high volume mass production, injection molding will be ideal for manufacturing this product.
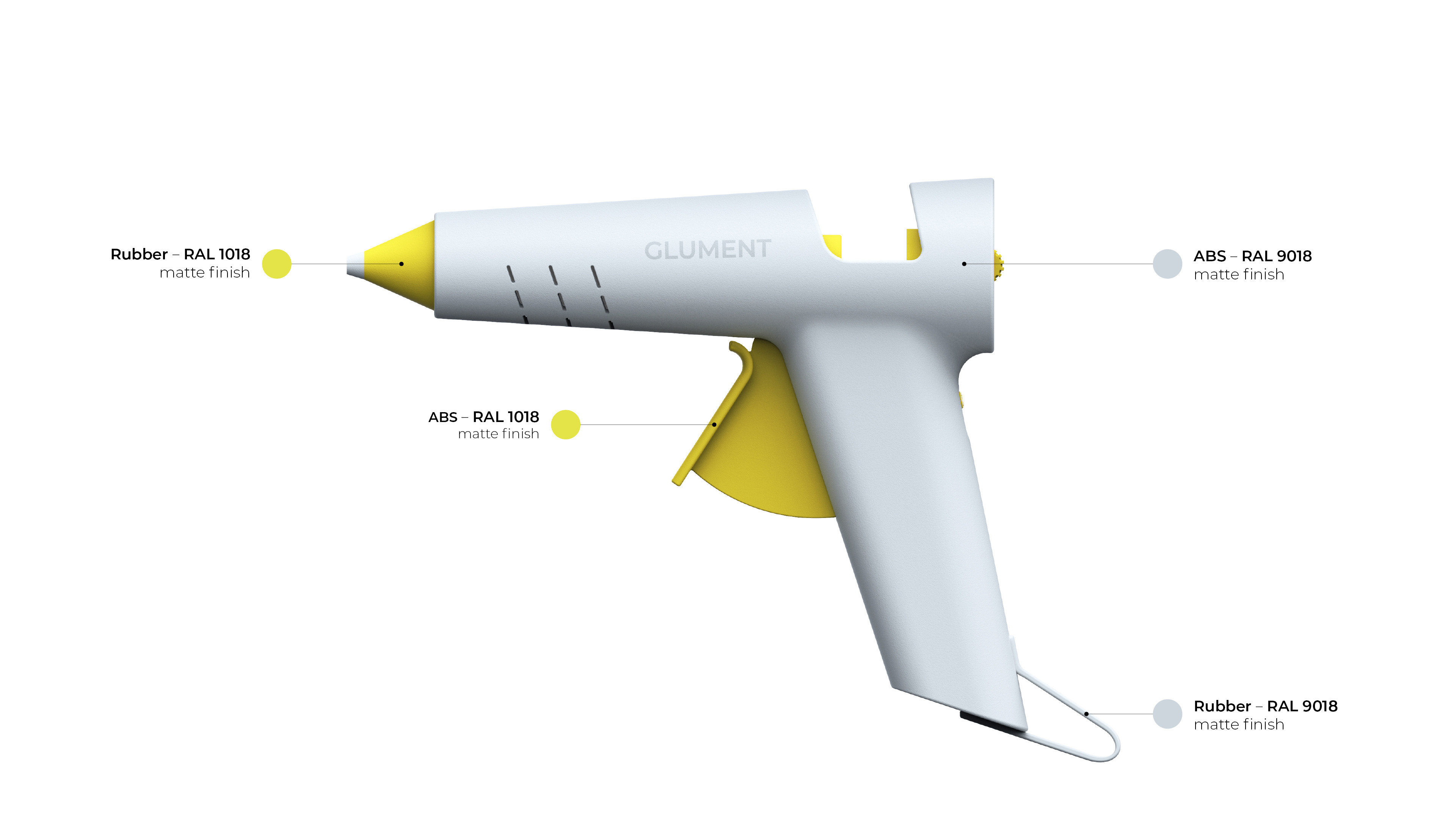
model making process
Each part of the hard model was 3D printed on Prusa i3 MK2 and then assembled.
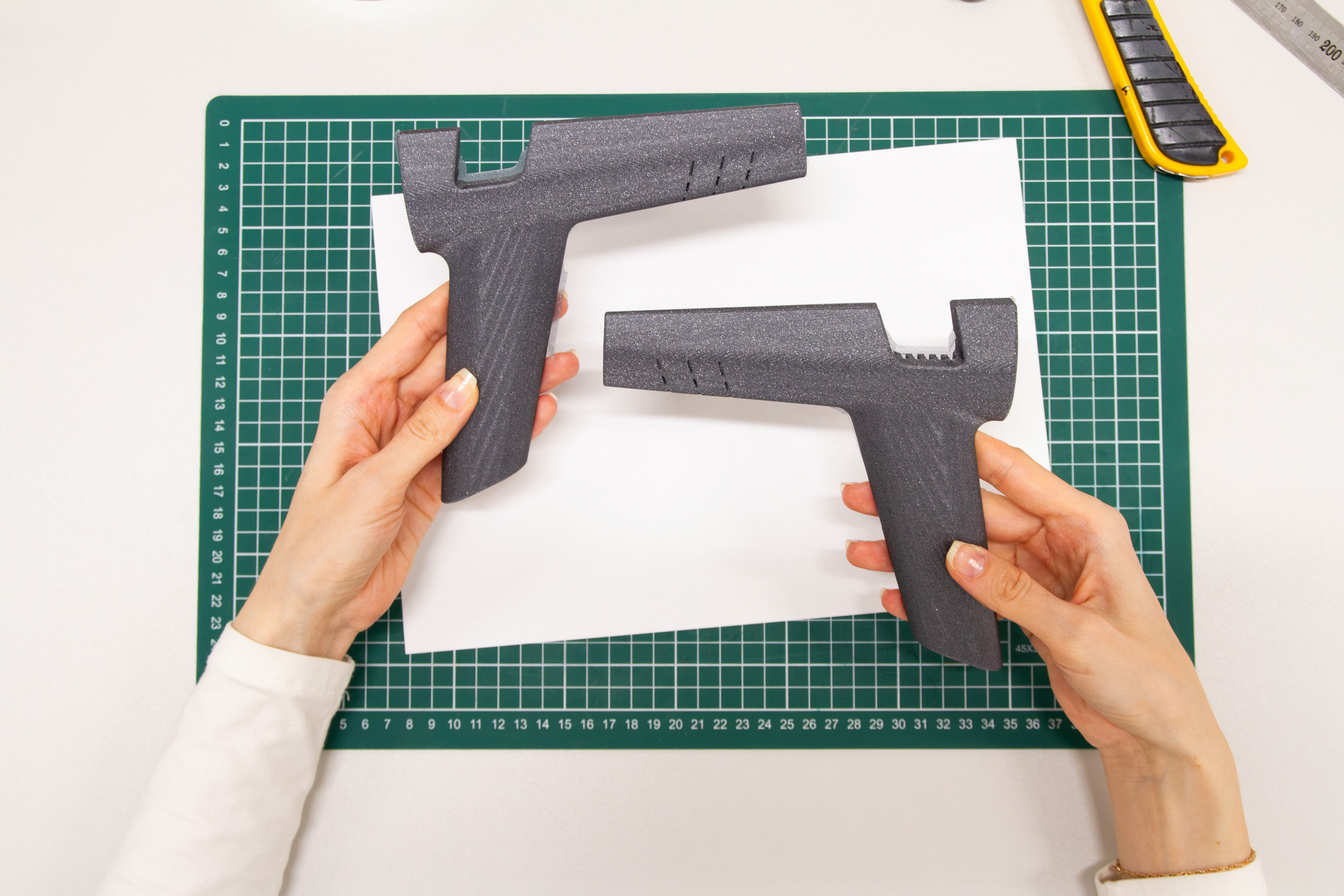
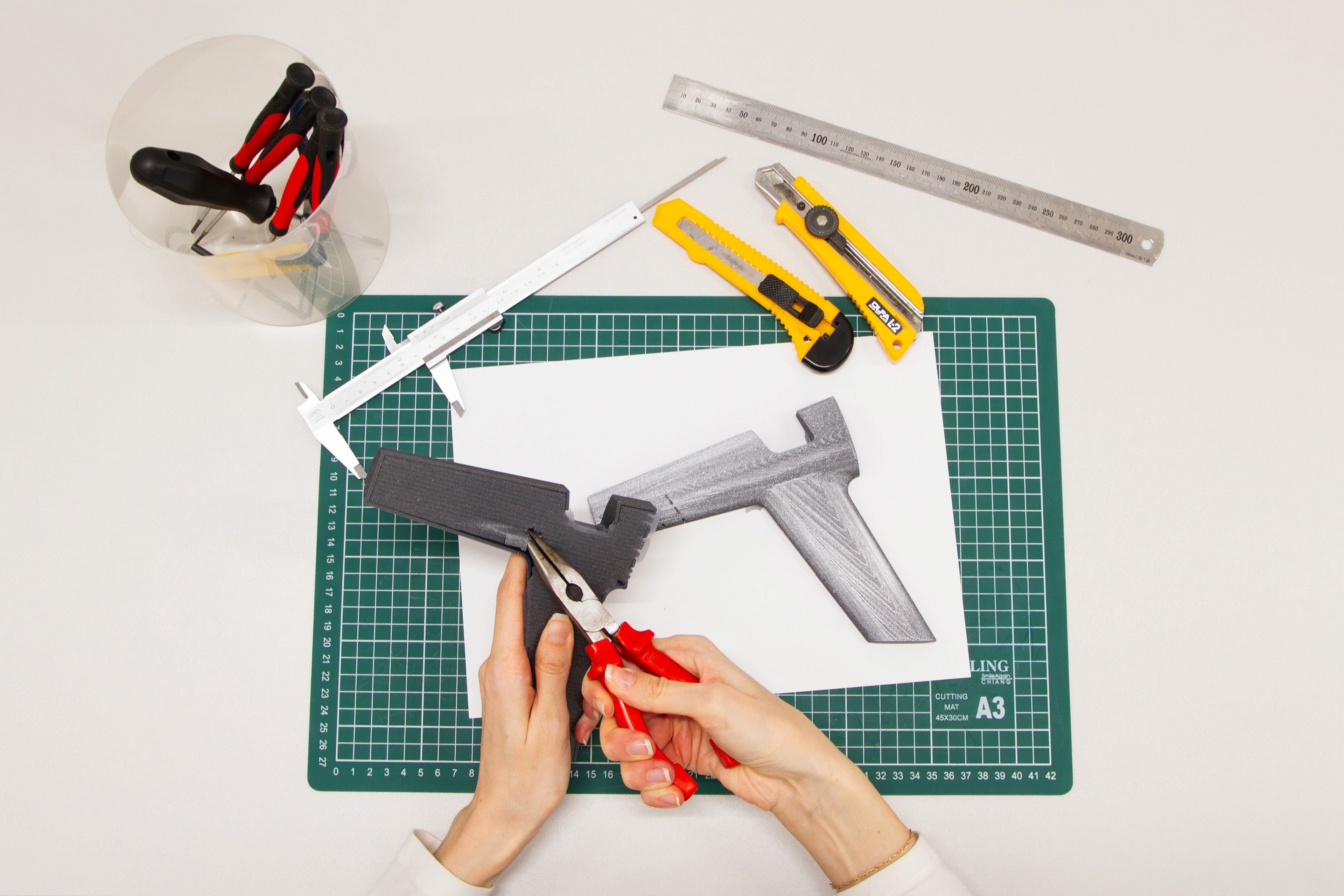
hard MODEL
Hard plastic model in a scale of 1:1 with a primer coat and no paint.
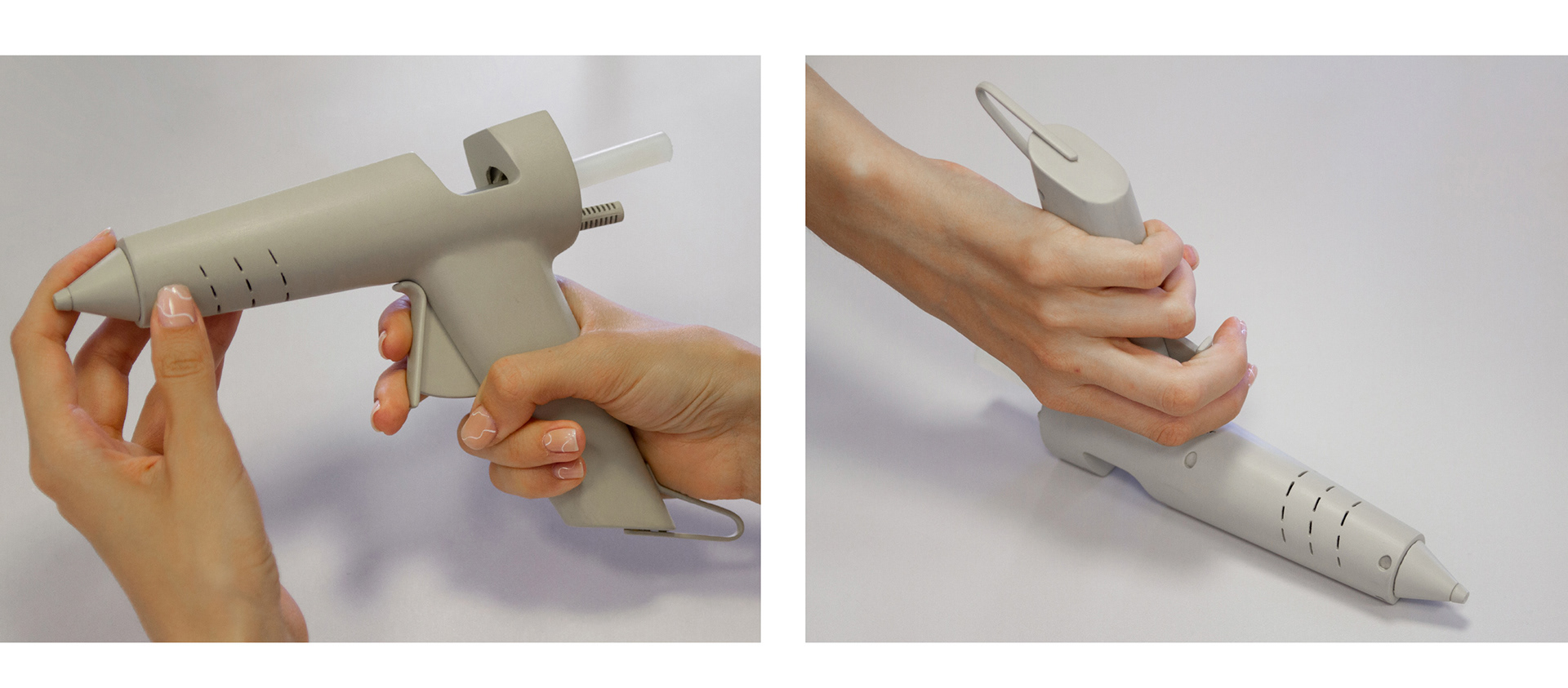
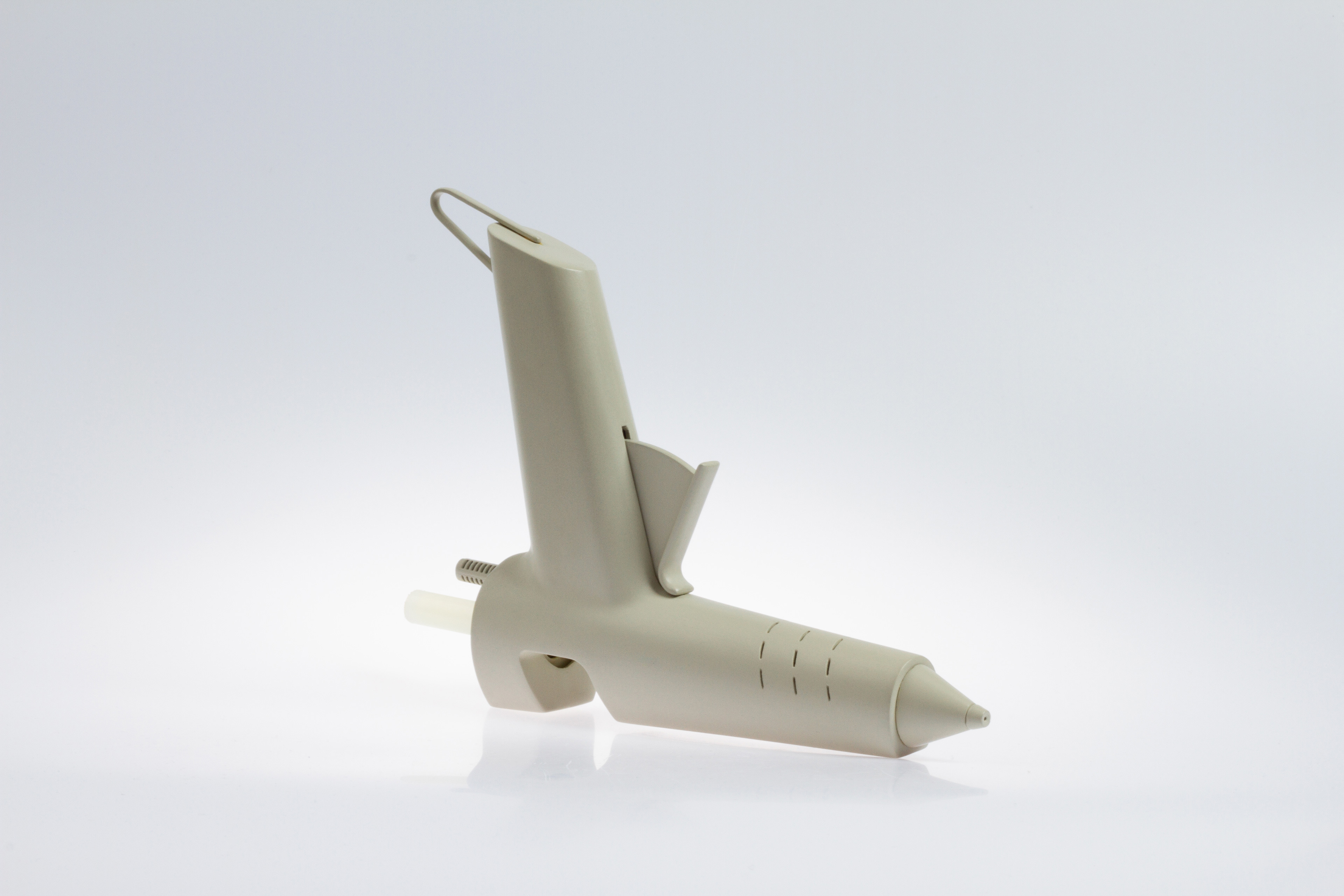
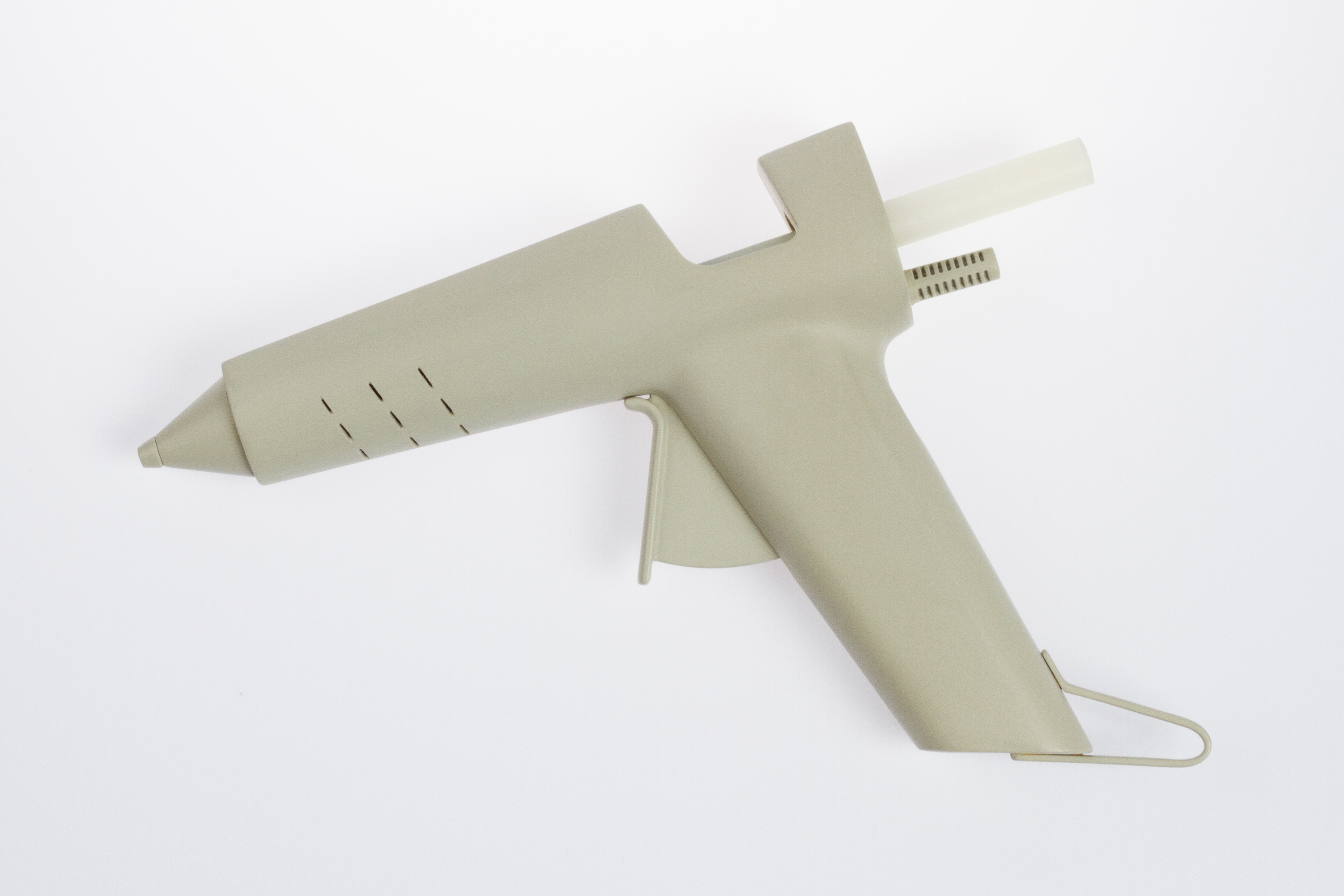
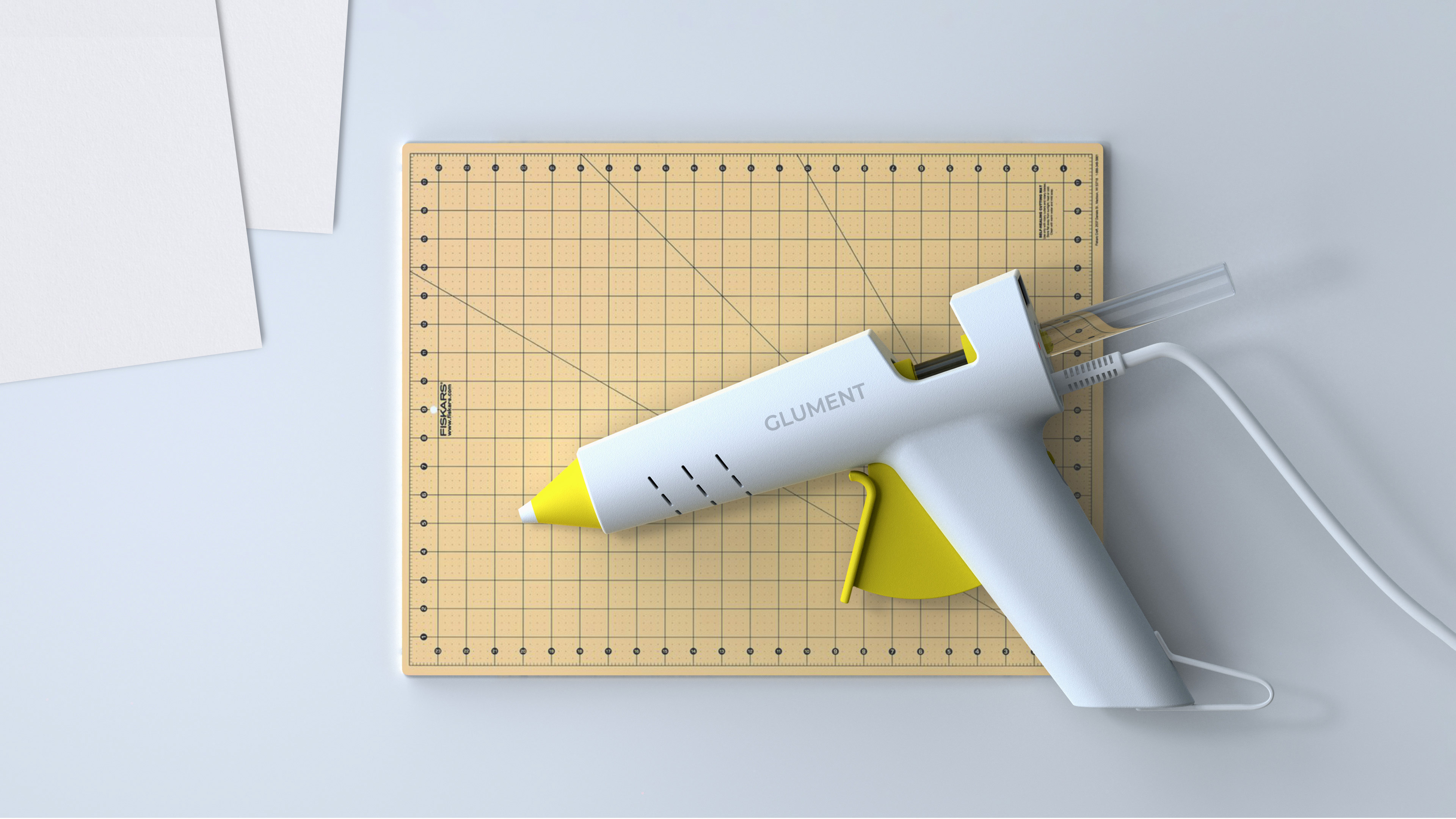